Companies face a complex landscape when selecting logistics software. While specialized applications promise to handle various aspects of supply chain and logistics management, the sheer variety often leads to a fragmented technology stack.
Companies may find themselves using one software for warehouse management, another for transportation, and yet another for inventory tracking.
A recent survey showed that 67% of supply chain professionals consider Excel to be a supply chain management software, an approach that can leave key information dispersed across multiple spreadsheets. This scattered approach creates integration challenges, making it difficult to have a single, unified view of operations.
This multi-software environment not only raises the operational complexities but also increases costs substantially. Each software comes with its own licensing fees, service fees, and learning curve. As a result, instead of streamlining logistics processes, companies may find themselves burdened by the very technology meant to simplify their operations.
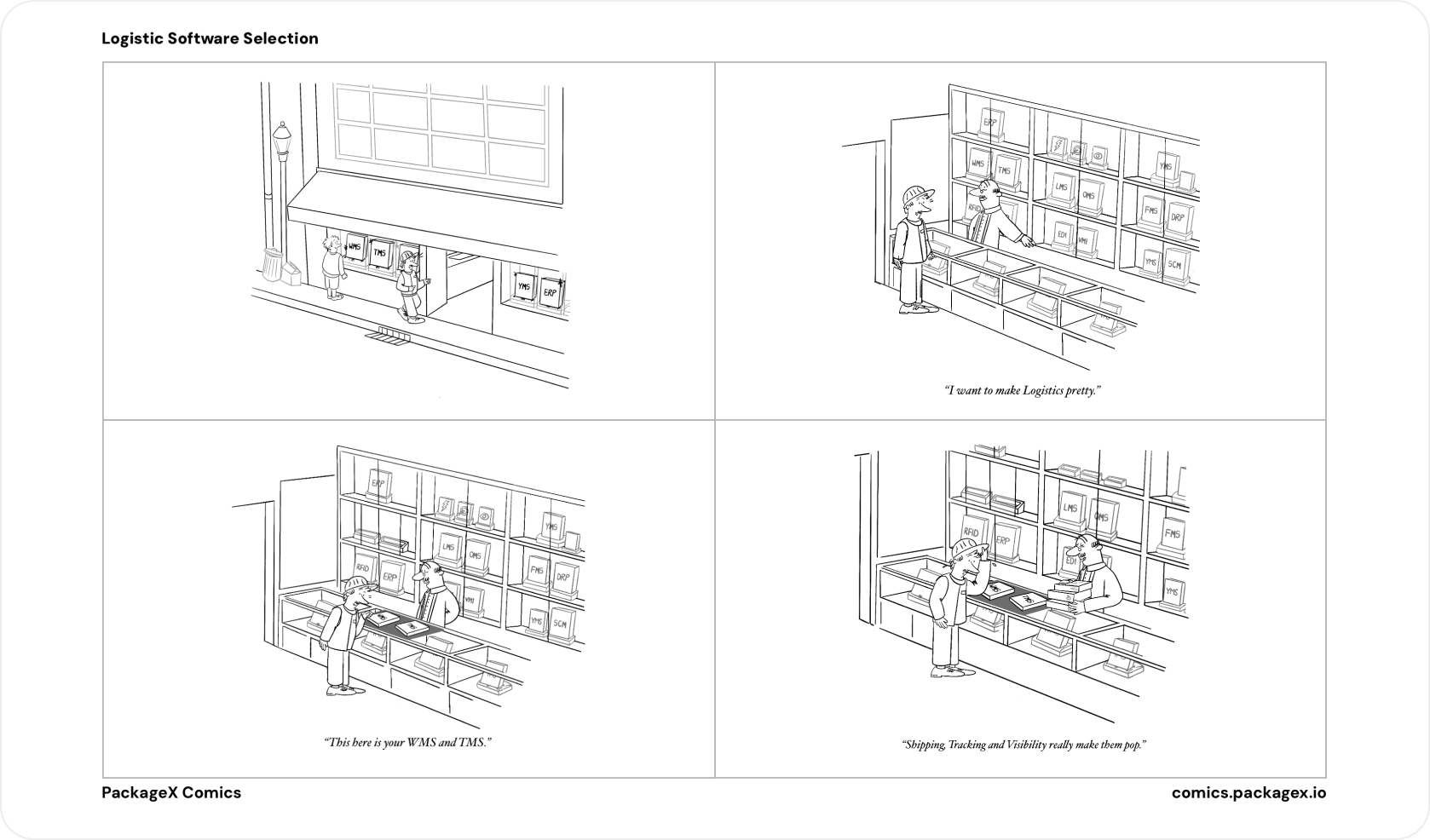
How to select the right logistics software
"Every company needs to think globally about their business, and strategically about technology.” ~ Daniel Stanton, Mr. Supply Chain
Step 1: Identify your software needs
Planning up front can save you from a reactive bolt-on approach down the road. Which logistics operations are manual? Where are you lacking visibility? And finally, what operations do you want to automate to get smarter for you business and customer? Think about priorities now and later. Reducing supply chain costs from 9% to 4% can double profits so don’t overlook this step. Correlate your business goals with your software needs to save yourself time and effort in the long run.
Step 2: Shortlist modular logistics platforms
Look for platforms that have APIs for easy customization and migration. These are more cost-effective since you’ll only pay for features you use, rather than rushing to find new software as issues arise.
Step 3: Select the most unified platform
Ideally, the logistics modules/APIs should all be connected on a platform where operators and admins can easily interact with data and make no-code configurations. The more integrated the platform is, the less time you’ll have to spend putting out fires with new and expensive software.
Step 4: Choose a platform that enables automation
The solution that will make the biggest impact on your business will prioritize data digitization at every logistics operation. Data digitization vs, capturing it on a piece of paper, spreadsheet, or within a soled legacy system, is a prerequisite for automation.
Which logistics software to avoid
“Companies must look at skills relevant for the new normal. What made us successful yesterday may not be what takes us forward.” ~ Kris Timmermans, Supply Chain Management Review
In Q2 of 2022, J&J snack foods lost an estimated $20 million in revenue after a transition to a new ERP led to “picking and scheduling issues.” This is, sadly, typical. Three quarters of ERP transitions go over schedule or budget, and two-thirds bring a negative return on investment.
Mission Produce faced a similar challenge this year when they were hit with a $4.1 million operating expense increase after an ERP transition. ERPs are a great system of record, but they can’t be relied on to deliver logistics efficiencies.
If you’re looking for a better software solution for your company, avoid bolt-on software that fills in for a shortcoming of your current logistics software.
For example, if you have outdated supply chain software, visibility software that gives you insights into where shipments and inventory are in your chain will not be included in the total package. If visibility is not included in the core supply chain software, it’s best to switch to avoid piling up tech debt.
To ensure you’re not taking on too much at once, request demos and trials. Getting hands-on experience with a variety of different tools can offer you a window into a tool’s functionality before you commit to it. Also don’t overlook total cost of ownership (TCO) which includes ongoing licensing fees, maintenance, customization, and training costs. Ignoring the full financial picture can lead to budget overruns and financial strain.
{{returns-webinar}}
How to transition to a unified logistics platform
Michael Hill, a Commonwealth jewelry company operating in Australia, Canada, and New Zealand is a supply chain transition success story. Three years ago, realizing that they needed to optimize their shopping experience, they brought their whole supply chain under one software umbrella. They launched an internal operation to streamline their entire supply chain and never looked back.
“The really exciting part is how fast we can adapt to changing business needs. We are driving efficiencies in our warehouse, trialing new fulfillment models, and unlocking deeper insights into customer experiences faster than ever before.” ~ Ian Dallas, Program Manager of Supply Chain and Finance @ Michael Hill
Transitioning to new software can be complex, but there are several steps you can take to make it less daunting:
- Set clear goals and objectives. Draft a detailed project plan that outlines the scope, goals, timelines, and responsibilities involved with the software transition.
- Use the strangler fig pattern. Choose one feature at a time (Inventory application for example) to move from your old platform to the new platform. If this experiment is successful, move more features to the new platform.
- Work closely with the software provider. Configure the new system to match your specific business needs. Customize workflows, reports, and user interfaces so that your organization can hit the ground running with the new software.
- Continuously monitor performance. Gather feedback from users within your organization and make necessary adjustments to optimize its ease of use and address any issues that arise.